設計者がついついやってしまいがちな代表的な設計ミスを紹介します。これまでの私の設計経験を元に、頻度の高いもの10項目を選出しました。今現在構想設計中のあなた、出図を控えているあなた、もしくはこれから設計を始めるというあなた。是非とも、本記事を参考に自分の設計を見直してみてください。
私はTwitterで定期的に情報発信を行ってますが、本記事はその発信の内容をまとめたものになります。私のTwitterをフォローしてくれている方は見たことある内容かもしれませんが、復習だと思って読んでいただければ幸いです。
これらの失敗は全て、私が実務の中でやらかしたものです。ポジティブに言い換えるなら、"生きた失敗"だと言えるでしょう。私の失敗から学びを得て、それをあなたの設計に活かしていただければ幸いです。それではいきましょう!!
配管・配線
配線・配管関係のミスはボディーブローのようにジワジワと効いてくるのが特徴です。最初は問題なくても、客先に納入してから数年後に一気に噴出します。しかも、そのほとんどがマシンダウンに繋がるトラブルになるため、要注意です。
油圧ホースの脈動

油圧ホースは、圧力が掛かるたびにビクッと動くような動作が起きます。これは"脈動"と呼ばれる現象です。この脈動により、ホースが動いてしまい、鋳肌や板金の角などと擦れることがあります。塵も積もれば山となる、ではありませんが、脈動により少しずつ削られた油圧ホースが、圧力に耐え切れなくなり破裂してしまうというトラブルも多いです。
ホースが脈動しても干渉がないような余裕のある取り回しが理想的です。それができないならホース保護を追加したり、板金の曲げ部で受けたりすると良いでしょう。また、油圧ホースと一緒にタイラップで取りまとめた配管類があれば、油圧ホースにつられて脈動するため同様の注意が必要です。
この手のミスは客先に出てから数年後に発覚することが多いので、設計ミスの不発弾とも言えますね。とにかく油圧ホースを見たら「こいつ・・・動くぞ!」と思って、設計をすることが大切です。
ケーブル最小曲げ半径の確認

配線・配管には必ず“最小曲げ半径“という仕様が必ずあります。これは、どれだけ曲げて良いかという指標であり、しっかり守らないと配線・配管の破れや破裂に繋がります。なんでも好き勝手曲げていいというわけではないんですね。
また、配線・配管を固定で使うか、可動で使うかでも最小曲げ半径の値は変わってきます。
固定・・・固定されていおり曲げ半径が変化しない
可動・・・可動物に付くため周期的に曲げ半径が変化する
仕様を正しく把握して、適切な取り回しや保護を行いましょう。特に電線の曲げ半径などは、適切に守らないと発火の危険性もあります。細心の注意を払いましょう。
オイルシール・Oリング
水漏れ・油漏れはどの機械に置いても頻発するトラブルです。その原因となるのが、オイルシールやOリングの損傷です。機械を使用していくうちに摩耗や劣化を起こし損傷することもありますが、組立時に損傷させてしまうパターンが結構多いんです。組立時のシール系の損傷は組立作業者の技能の問題ではなく、実は設計の問題だったりもします。気をつけましょう。
Oリングの基礎ついては、別記事でまとめてまとめていますので合わせてお読みいただくことで、より一層理解が深まります。
オイルシール部の面取り

組み立て時のOリング切れ防止のため、15~30°の面取りが必要です。忘れるとロッド挿入時などにOリングが切れたり、亀裂が入ったりして、油漏れの原因になります。オイルシールメーカの推奨条件もありますので、詳しくは各メーカのホームページを見たり、直接問い合わせたりすると良いでしょう。
もちろん面取りを忘れたからといって、必ずOリングが切れる訳ではありません。逆に言えば、既に生産している機械でも「なんかOリングがよく切れるんだよなー」と言われている箇所があったら、そういう個所は面取りが取れていない可能性がありますね。既存機の流用をするときも丸々鵜呑みにせず、注意深く見てみましょう。個人的な感覚では、この面取り忘れは新入社員がやりがちな設計ミス第一位です。
Oリング溝の配置

Oリング溝を検討するときは、その部品を組み付ける際の"天地の関係"を意識しましょう。当然、場所によって出来る出来ないがあると思いますが、可能な限り地側に溝を付けることが大切です。組み付け時のOリングの脱落防止になります。
天側にOリングがあると、取り付けの際に脱落するリスクがあります。しかもこういう部分って、脱落に気が付かずに組み付けてしまうことも多いです。そして機械が完成してから、油漏れを起こして気が付く・・・という王道パターンですね。脱落しなくとも、噛み込みの原因にもなります。組立作業者が神経を擦り減らすことになるため、Oリングは地側に配置してあげるのが設計者として必要な配慮です。
また実際の機械の姿勢と、組立時の姿勢は反転していることがあるので、組立工程を把握した上で決めましょう。CADで見ている姿勢が組立の姿勢だと勘違いしてしまうことはよくあります。イメージで判断せず、現場を見に行く癖をつけると良いでしょう。
色々な干渉
もはや"干渉"は機械設計者の永遠のテーマですね。昨今では、3DCADが普及してきたこともあって、昔ほどの致命的なかなり干渉は少なくなったと言われています(当社比)。逆に、現場からは3Dで設計しているのになんで干渉をゼロにできないの?なんて言われたりもします。おそらくこれを読んでいる設計者の方々にとっても非常に耳の痛い話ではないですかね。
ドラフターで下積みした歴戦のおじいちゃん設計者曰く、「3DCADに頼ることで、3Dモデルには現れていない”現物とのギャップ”を見逃すことが多くなった」とのこと。言われてみれば確かにそうなのかもしれませんね。ここで紹介するのも全てそういう事例です。
作業工具の干渉
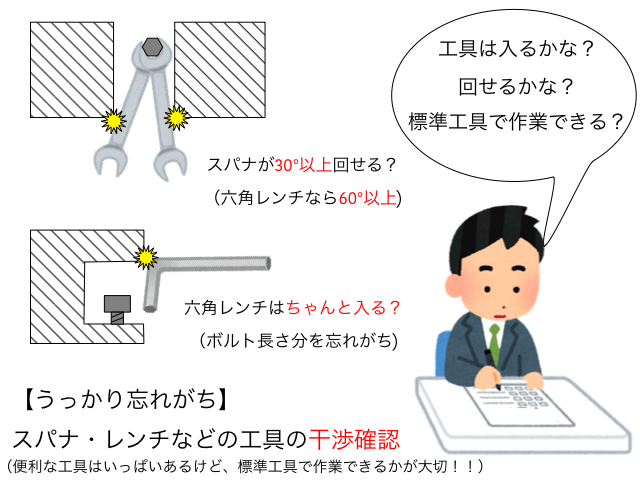
スパナやレンチといった作業工具がしっかりボルトに届いて作業できるようになっていますか。CADで設計していると、どんな場所でもボルトを配置できてしまいます。しかし実際は工具が届いて、作業できるスペースが必要です。作業スペースは確保できているか、事前に検証しましょう。
スパナなら30°、レンチなら60°回すだけのスペースが必要です。ラチェットのエクステンションやカットレンチなど、便利な工具は沢山ありますが、一般的に出回っている標準工具で作業できることが大切です。自社工場なら工具は潤沢にあると思いますが、サービスマンが客先で保守する場合は限られた工具しか持っていけません。それ故に、一般的な工具で作業できる必要があるのです。
何を標準工具として定めているかは、各社規定が異なると思います。自社の規定をしっかりと把握しましょう。大きなお世話かもしれませんがそういった規定がない会社は、しっかり作った方が良いですね。
購入品の3Dモデル確認

3D CADを使って設計している場合の話ですが、購入品のモデルの寸法が正しいか確認しましょう。サプライヤーから提供される3Dモデルは厳密に作られていないことがあります。気軽にネットからダウンロードできますが、鵜呑みにしてはいけませんよ。3Dモデルだけを信じて設計を進めると、実物が出来たときに致命的な干渉を起こしたりして、非常に痛い目を見ます。私も最近、このミスをしました。かなり致命的な部分の干渉で、大幅に改造しましたね。あまりに致命的過ぎて、タイムマシンを設計して過去に戻った方が早いんじゃないかと思ったほどです。
基本的には購入品の寸法は、取り交わした仕様書に書いてあることが全てです。3Dモデルはあくまでも参考扱いなので、仕様書に書いてある寸法通りにモデルが作られているかを絶対に確認してください。大切な事なので、もう一度言いますが購入品は仕様書が全てです。
溶接ビードとの干渉

溶接がある部品でも、3Dモデル上では溶接ビードを表現していない場合があります。しっかりモデルを作りこんでいる会社もあるようですが(本当はそれが望ましい)、表現しないのが一般的だと思います。実物を作ってみたら、溶接ビードと部品が干渉して取りつかなかった、なんてことは頻繁にあります。(機械設計あるあるの中でも、かなり上位に食い込みますね。)
干渉が発生する度に、現場に頭を下げてビードを削り取ってもらうわけです。しかし、溶接の仕方によってはビードを削り取ってしまったことで、その後に溶接剥がれの原因になる場合もあります。リカバリーの工数も掛かるため、設計段階でしっかりと潰しておくのが大切です。
溶接部分をしっかり把握して、ギリギリまで攻めずにクリアランス5~10mmくらいを確保しておくようにしましょう。
組立・調整
組立や調整を行う際にトラブルになる設計ミスを紹介します。“後工程はお客様“という言葉があるように、ものづくりの上流工程に属する機械設計は、実際の機械ユーザ以外にもお客様がたくさんいます。後工程目線で設計を考えることが望ましいですね。かくいう私も、なかなか上手くはできていませんが・・・。そんな組立・調整性に関わる設計ミスを紹介します。
工具Rとの干渉

3Dモデル上ではピン角でも、実際の加工品には必ず"工具R"が付いてきます。面をピッタリと当てようと思ったら、工具Rを逃がすための面取りやヌスミが必要になります。この工具Rに部品が担いでしまうと、部品が傾いて取りつくことになるため、機械の精度が狂ってしまいます。インロー部などは特に注意して確認しましょう。
ちなみにこれは私が設計を始めて、最初にやった設計ミスですね。組立後の動きの精度が悪くて、分解して調査してもらったら発覚しました。現場の方に"ここで工具Rを担いでるからヌスミがいるぞ"って言われましたが、"工具R"も"ヌスミ"も意味を知らなかったので、必要な工具を誰かが担いで盗んで行ったのかと思いました。
吊り位置の検討

吊りは安全に関わる重要な作業です。部品単体で安定して吊れることは当然ですが、アセンブリ単位でもしっかりと安定して吊れるように設計しましょう。そのためには、組立工程を正しく把握する必要がありますね。部品単体では吊れたけど、組み立てたら吊穴が隠れてしまった、なんてミスも良く見ます。常にどう組み立てるかを頭の中でシミュレーションしながら設計する癖を付けましょう。
また、吊穴があってもアイボルトが付かないというミスもあります。アイボルトのアイが干渉しない分のクリアランスも意識して設計しましょう。
ボルトの掛かり代の確認
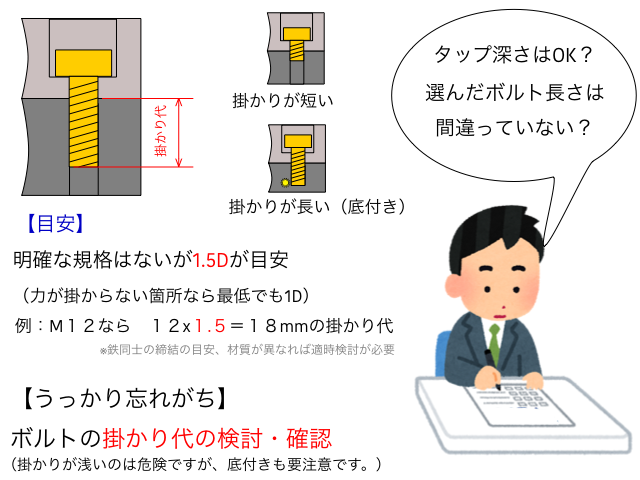
ボルトが正しい締結力を出すためには、適切な掛かり代が必要です。タップ深さとボルト長さの関係はしっかりと検討しましょう。特にタップに対して、ボルトが長すぎると、ボルトの底付きを起こします。際どい長さだと、底付きしたことを締め込んだと勘違いしてしまうこともあります。そうなると、締結されないまま機械が作られてしまうため大変危険です。
ちなみに私は機械の駆動系部分でこのミスをしたことがあります。あまりに動きがガタガタなので、おかしいと思ったら、駆動系のボルトが全て底付していたんです。締結されていない部品は、動かすたびに通し穴分のガタで揺れていました。その衝撃で半分くらいのボルトは頭が吹っ飛んでしまっていましたね。非常に恐ろしかったです。
ネジ部の掛かり代には明確な企画はありませんが、感覚的には最低1.5Dは取った方が良いでしょう。DはdiameterのDで、ボルトの直径のことです。例えばM12のボルトであれば、M12 x 1.5=18mm以上の掛かり代があると良いという計算です。参考にしてください。
まとめ
本記事の内容を復習しましょう。
・油圧ホースの脈動
・ケーブル最小曲げ半径の確認
・オイルシール部の面取り
・Oリング溝の配置
・作業工具の干渉
・購入品の3Dモデル確認
・溶接ビードとの干渉
・加工品の面取りヌスミ指示
・吊り位置の検討
・ボルトの掛かり代の確認
冒頭にも書きましたが、ここで紹介したミスは全て私が実際に起こした設計ミスです。実体験を元に書いたので、内容としては血の通ったものになっていると自負しています。技術的にレベルの高い話ではなく、ちょっとした意識で気がつける事ばかりですよね。でも、機械設計の実務ってこういう部分が非常に重要だと思います。神は細部に宿るものです、細かいことの積み重ねがより良い機械を作り出していくんだと思っています。本記事が今後のあなたの設計を見直す機会になれば幸いです!
その他、設計の参考になる記事をいくつも書いているので是非合わせてお読みください。
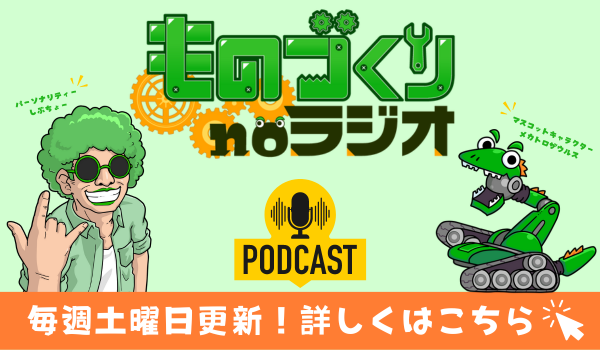
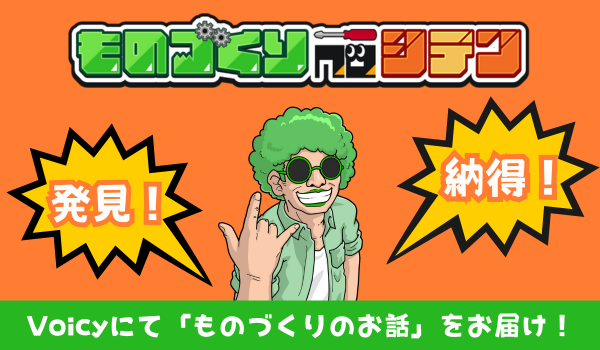