失敗から学べることは多くあります。例えそれが自分の失敗でなくても、失敗を考察することで教訓を得ることができます。そこで今回は設計失敗事例を紹介し、そこから学べることを考察していきたいと思います。
ドイツの政治家オットー・ビスマルク氏は「愚者は経験に学び、賢者は歴史に学ぶ」というの言葉を残しています。それほどの過去の失敗というものは財産なんです。本記事で、過去の歴史的な失敗事例から教訓を学び、あなたの設計ノウハウとして活かしましょう!!
今回取り扱うのは、機械設計における"規模の限界"の話です。既存の機械を、"もう一回り大きくしよう" なんてことはよくありますよね。例えば、既に生産している機械の機種展開機として、既存機の2倍の大きさの機械を設計しろと指示があったとします。あなたは、既存機の寸法をそっくりそのまま全て2倍の大きさにすれば設計は成り立つと思いますか。機械設計者ならば、これが成り立たないのはなんとなくわかると思います。では、なぜこの単純なスケールアップの設計が成り立たないのか、その理由を説明することができるでしょうか?
本記事を読むことで、その理由を論理的に説明することができるようになります。既に理由がわかる人も復習がてら是非、目を通してみてください。それではいきましょう!
歴史的な失敗事例を見てみよう
古代ギリシャの設計家に、ディオグネトゥスと男がいました。なんて呼びにくい名前なんでしょう・・・、まあそれはさておき、彼はロドスという都市に住んでおり、この都市を戦争から防衛するための兵器や策略を考えるのを生業としていました。ディオグネトゥスの防衛の手法は、目新しいものではなく古典的な手法ではありましたが、長きにわたり都市を守り続け、その実績により民衆から強い支持を得ていました。
ある日のこと、カリアスという男が突然ロドスの街にやってきました。カリアスは民衆に対して、自分が設計した新型兵器の模型を披露します。
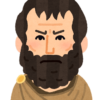
これは敵のどんな攻城兵器でも捕まえることができる無敵の回転起重機(クレーン)だ!
カリアスは豪語しました。回転起重機の模型は、精巧かつ動きまで厳密に再現しており、非常に高いクオリティでした。ロドスの人々は、その素晴らしい設計に感銘を受けました。カリアスは大きな期待を集め、逆に旧来のやり方しか知らないディオグネトゥスは徐々に信頼を失っていきました。そして、ついにディオグネトゥスに与えられていた権威や実権は剥奪され、全て“カリアス“に与えられることになったのです。
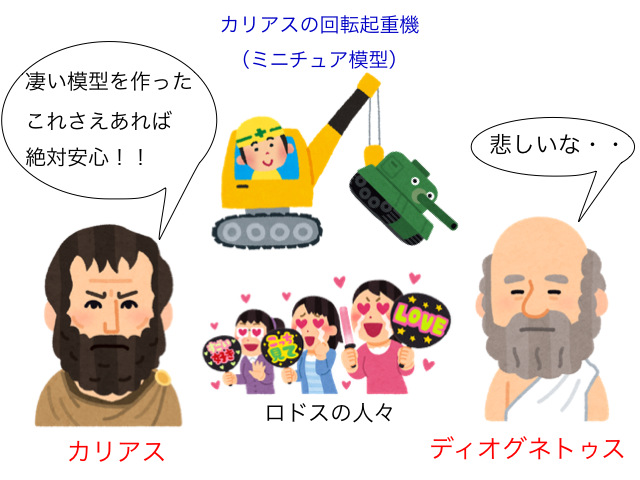
そして時は満ち、近国との戦争が始まりました。近日中に敵の巨大兵器が攻め込んでくるぞ・・・という段階に差し掛かります。しかし、ロドスの人々には余裕があります。何故ならカリアスが設計した無敵の回転起重機があるからです。カリアスは国から回転起重機の模型を実際のサイズで作り、対抗するように求められます。しかし、カリアスは衝撃の一言で支持者たちを驚かせます。
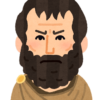
模型は上手くできましたが、実際の大きさは作れません・・・
は?
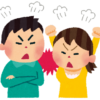
模型ではあれだけ素晴らしい設計であったにも関わらず、カリアスは実際の寸法で回転起重機を作り出すことは不可能だと言い放ちました。そう、ロドスの人々はカリアスの間違った推論に欺かれていたのです。困り果てたロドスの人々は、ディオグネトゥスに泣きついて、助けを求めました。実権を剥奪されたことで深く傷ついていたディオグネトゥスは、一度は彼らの頼みを断りました。しかし、ロドスを守るため再び立ち上がり、最終的には見事にロドスの都市を防衛することに成功します。
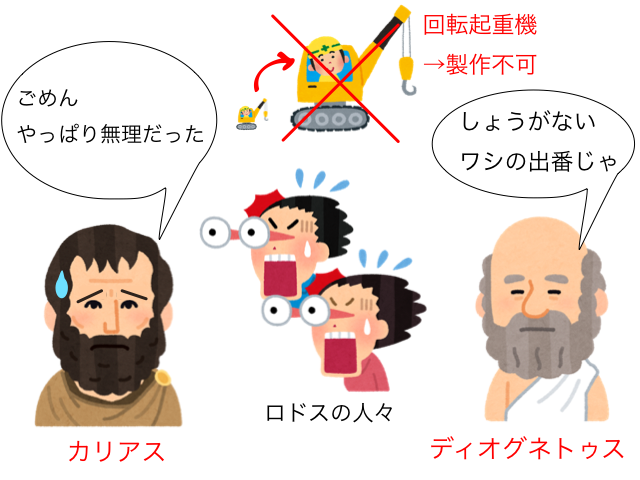
敵は退散し、ディオグネトゥスは再び栄光を授かりまリた。カリアスがその後、どうなったかは知る由もないですが想像に容易いですね。
なぜ模型を実寸法で作ることができなかったのか?
カリアスが、最初から模型を実際の寸法にスケールアップできないと知っていたのか、それとも途中で気が付いたのかは定かではありません。ここでは、模型を実際の寸法にスケールアップできなかった理由を考察していきましょう。
寸法と強度の関係
既に成り立っている機械をそのままの形でスケールアップしていくと、どこかのタイミングで必ず"強度不足"に陥ります。これが"規模の限界"というものです。形状を無限に大きくしていくことは不可能であり、かならずどこかに限界があります。
では、それはなぜなのか。これは単純な話で、大きくすれば当然強度も強くなりますが、それ以上に重くなるからです。強度の増加幅より、負荷の増加幅の方が大きいので必ずどこかのタイミングで限界を迎えます。
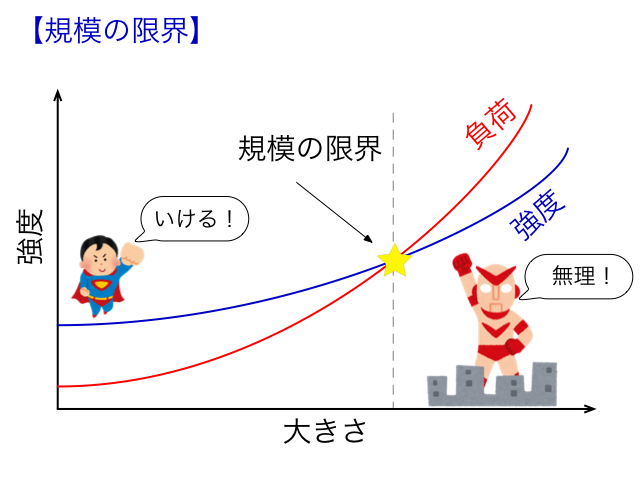
例えば、大きさを2倍にすると、強度は4倍になり、重さは8倍になります。大きさが3倍なら、強度は9倍、重さは27倍です。これは断面積と体積の関係で説明することができます。シンプルな片持ちの円柱で比較してみましょう。
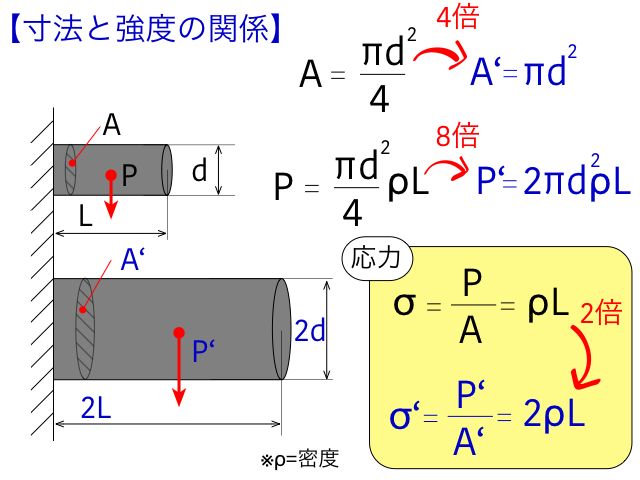
上図から、大きさを2倍にしたことで、断面積A(強度)は4倍となり、重さP(荷重)が8倍となっているのがハッキリとわかりますね。ここでの最大のポイントは"応力σが2倍"になっていること"です。
応力は部品内部に掛かる力を示す物理量で、荷重/断面積で表すことができます。応力には許容応力という材料ごとに決められた値があり、設計者はこの許容応力を元に部品の形状やサイズを決定します。スケールアップを成り立たせるのであれば、スケールアップ後も応力が同じ値でなければなりません。円柱の例でわかる通り、応力は2倍になっているわけです。大きくすればするほど、部品に掛かる応力は増えていき、いつか必ず破損します。これこそが模型をそのままスケールアップできない理由です。模型サイズでは、応力的に問題がなく成り立っていても、実寸法にすると容易く材料の許容応力を超えてしまうのです。
かの有名なガリレオも、この規模の限界を説明する上で自然界を例にとり下記のような説明をしています。
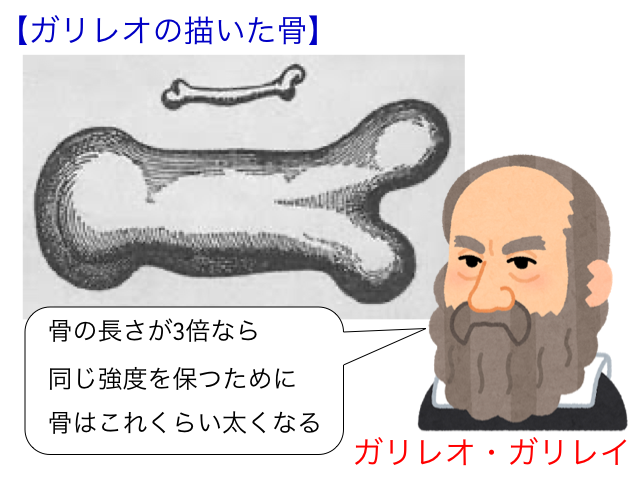
"骨の長さは三倍にしてあり、太さはこの巨大な骨に相応した太さにしてある。これだの太さにしておけば、小動物の小骨格と同様の程度に巨大な動物の骨格はその運動に役立つ。"
単純に3倍の大きさにして成り立つような強度にするならば、これだけ強烈な太さが必要だということです。これも上記した応力の話に基づくものですね。
実際の機械でみるなら、ショベルカーの写真を見比べると非常にわかりやすいです。巨大ショベルカーをミニショベルを同じ縮尺で比較したのが下図です。
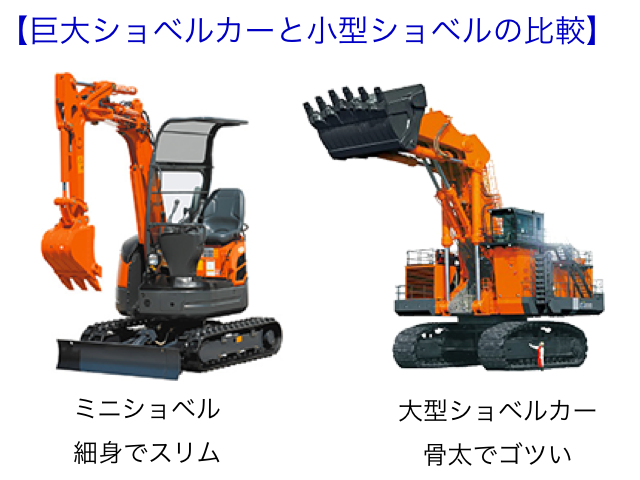
画像引用:日立建機日本
同じ縮尺にして見比べてみても、同じ形でないことが良くわかります。巨大ショベルカーの方が明らかに骨太であり、ミニショベルはスリムな印象です。これも規模の限界による形状の違いです。
製作上の問題
単純なスケールアップが成り立たないのは、上述の通り、規模の限界が主な理由です。
ですが、製造上の問題としてスケールアップが難しいという場合もあります。模型では如何にも作れそうな構造でも、実寸法のものとして作り出すのが物理的に難しいこともあります。例えば、カリアスが作った模型で部品の締結にM3のボルトが使われていたとしましょう。実寸法にするために、20倍大きくしようとした場合、この部分の締結はM60となります。それが既に現実的でないのはよくわかると思います。
これは極端な例ですが、今のサイズだから加工や組立をすることができたということも十二分にあり得ます。スケールアップには、必ず製造上の問題も付きまといます。これに関しては、設計者がスケールアップの際に形状を工夫すればいいのではないかと思うかもしれませんが、設計思想に関わる根本的な形状の変更をせざるおえないケースも多々あります。侮れない問題です。
私の失敗事例-ローラベアリングの予圧抜け-
機械設計者として働いていると、全く新しいものを作り出すという機会は実はそんなに多くありません。参考にできる過去の機種から、構造を踏襲したり、流用したりして既存の形を変更、そしてスケールアップする形で設計を進めることがほとんどです。当然、私も既存設計のスケールアップを経験してきました。その中で、思いもよらない失敗をしたことがありますので、ここで紹介しておきます。
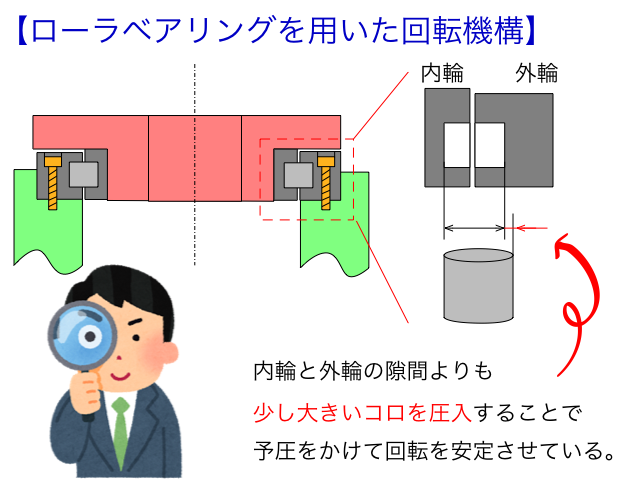
上図のようなローラベアリングを用いた回転機構を設計した際の話です。
高い回転精度を得るために、ローラベアリングには"予圧"が負荷されています。予圧の掛け方は様々な方法がありますが、このベアリングは寸法で予圧を掛けるタイプのベアリングでした。内輪・外輪の隙間よりも少し大きい径のコロが圧入されており、それでギュッと予圧を掛けてあるわけです。
同じ種類のベアリングは既存機種で既に採用実績がありました。その時は、より大きいサイズのベアリングが必要だったので既存機種より大きいものを選定しました。スケールアップ案件だったので、特に部品の強度検証を念入りに行い、慎重に設計を進めていきました。大きいベアリングなら、当然発熱も大きい。そう考えて冷却系統にもかなり気を使いました。
そして、いざ実機を作って運転したところ、ある程度回転させたところで突然、異音が発生ました。当然、試験を中断し原因を探ります。色々と調査を進めていく上で、原因はベアリングの予圧抜けであることを突き詰めました。予圧抜けとは、簡単に言えば内輪・外輪・コロの間に掛かっていた予圧が何らかの理由で抜けてしまい、ベアリングがガタガタの状態になってしまうことです。
では、なぜ予圧抜けが起きてしまったのか。それは、ベアリングが発熱することで、外輪が膨らんで予圧が抜けてしまっていたのです。
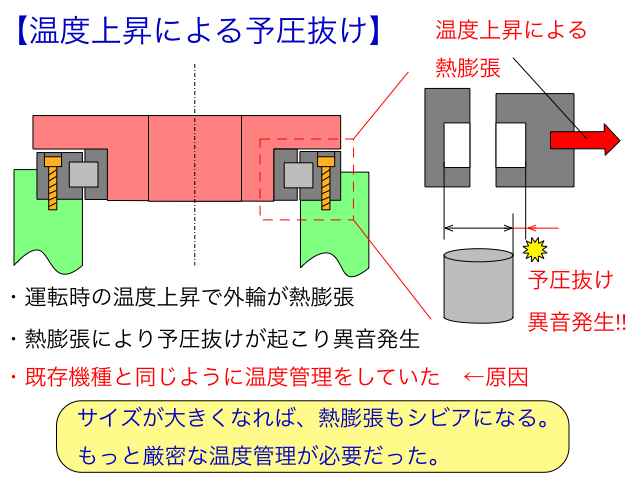
冷却系統にもかなり工夫して、既存機種と同じ温度でコントロールできるようにしたのに・・なぜ?私は頭を悩ませました。そこでハッと気が付きました。
"既存機種と同じ温度でコントロールできるようにしたのに・・・・"
これがそもそも間違いだったのです。ベアリングが大きくなったということは、同じ温度でもより大きく変形することになります。"1℃、1m、12μm"という言葉は有名ですね。1mの鉄が1℃温度が上がったら12μm寸法が伸びるというものです。同じ1℃であっても、元の寸法が大きければ変位量も寸法に従い大きくなります。その単純な原理に気が付かず、小さいベアリングを使った時と同じ温度でコントロールしようとしたため、予圧抜けの不具合が発生していたのです。
何とか冷却回路の対策して、無事に機械は動くようになりました。スケールアップの設計は、思わぬリスクを抱えているということを学ぶよいキッカケになりました。
まとめ
本記事の内容を復習しましょう。
・単純なスケールアップが成り立たないのは、規模の限界があるから
・モノを大きくすると、強度も上がるが、それ以上に負荷が大きくなるから
この記事で私が伝えたかったのは、"安易に大きさを変えるのはリスクがあるから気をつけろ"ということです。機械設計に携わっている人なら今回の話は当たり前だと思うかもしれません。そもそも模型をスケールアップすることなんてないし、既存機種を流用するときも設計検証しているから大丈夫と。
私もスケールアップのリスクはわかっていたつもりでしたが、上述のような設計の失敗をしました。スケールアップに潜む思わぬ落とし穴。サイズが変われば設計検証が必要な項目も変わるのです。是非ともこれを肝に銘じておいていただきたいです。
また、実は最近、実物を作る前に模型を作って検証してみようという取り組みが増えてきています。それはなぜか・・・そう、3Dプリンタが登場したためです。一昔前は、わざわざ模型を作るのはコストも時間もかかるため、現実的ではありませんでした。ですが、今となっては検証の一環として、3Dモデルを作ることも多くなってきました。そして、わざわざ重役が出席する会議にまで模型を持ち出してこう言うのです。
部下「これが次機種の構想モデルです、いかがでしょうか」
上司「おお、これは剛性がありそうでいいな、よし作ってみろ」
さながら、ロドスの人々とカリアスの関係のようですね。
(実物は作れませんとは口が裂けてもいえませんが。)
それが模型であっても"モノ"というのは相手を納得させるために最も有効な手段の一つです。このように、今後は模型を作ってから実物を作るという流れが普及するように思います。機械設計者である我々は、この圧倒的な説得力を持つ模型に惑わされてはいけません。何も難しいことは必要ありません。模型を見たら一つだけ
「本当に実際の大きさで作ることができるのか」
と疑いの目を向ける、それが大切なのだと思います。
本記事を執筆する上で参考にしたのは下記に二冊の本です。面白い本なので興味があれば是非、手に取ってみてくださいね!
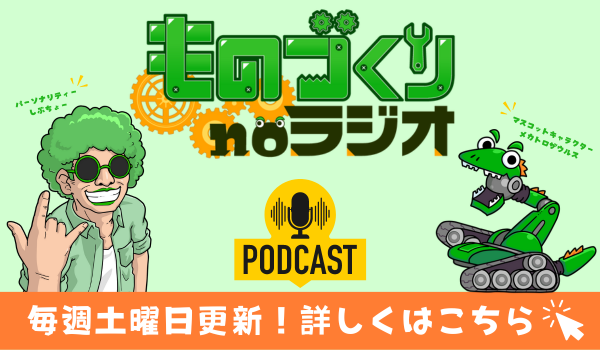
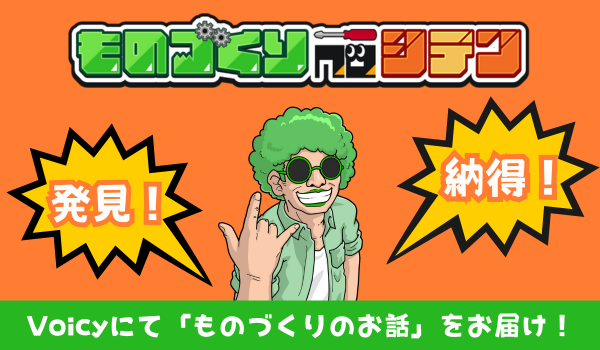